Located in ShenZheng is the R&D foundation of Studio Electronics. Composed of high-quality scientific and technological elites, the R&D team constantly introduces new technologies to strengthen the lineup of OEM products. They also cooperate fully with customers to improve product novelty and the living quality of consumers. Practical innovations require the R&D team to grasp the market pulse and further stimulate breakthrough ideas. With many years of rich experience in hardware and software integration, Studio's R&D team — on the premise of meeting customer demands — has further exceeded customer expectations of their original manufacturing conditions
Demanding perfection in design and sticking to the spirit of doing things right the first time, Studio's R&D team cautiously defines, purchases, inspects, and recognizes the specifications of various parts. This ensures the final product quality and finds problems and solutions during mass trial production. To assist customers in accelerating product launches.
The market demands a reliable, durable, and economical product. Backed by years of experiences in PCB and assembly, Studio engineers will interface with your team in the early stages of product development or manufacturing to provide the best solutions for quality and reliability performance, cost reduction and supply chain initiatives.
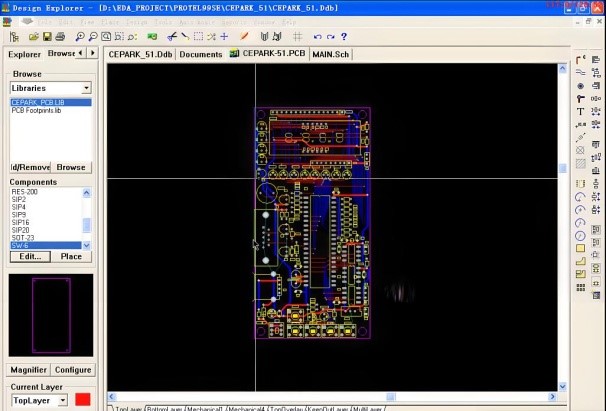 |
PCB Layout
Studio has the expertise to assist you with your PCB layout design needs, from new board designs to updating existing boards. We offer a full range of PCB design services from board layout to management of the board fabrication process, test and assembly with extensive design for manufacturing knowledge. Our PCB designers have many years of combined commercial and automotive experience ranging from high volume consumer single-sided boards through complex multi-layer digital to analog and RF designs. |
|
Design for Manufacture
DFM is critical to guarantee the product cycle, minimizes development cost and ensures a smooth transition into production from prototype stages. The first article approval is the initial most important step toward effective DFM. An OEM approved first article proves valuable in answering all questions relating to manufacturing, assembly and test. It is the “ proof of concept ” before going into production, even if quantities are small. The first article ensures that the transition into production volumes is smooth with few to no questions left unanswered. Plus, for the OEM, smooth transition to production means key market demands such as time-to-market, quality, reliability, product delivery, and the very critical time-to-revenue are met. |
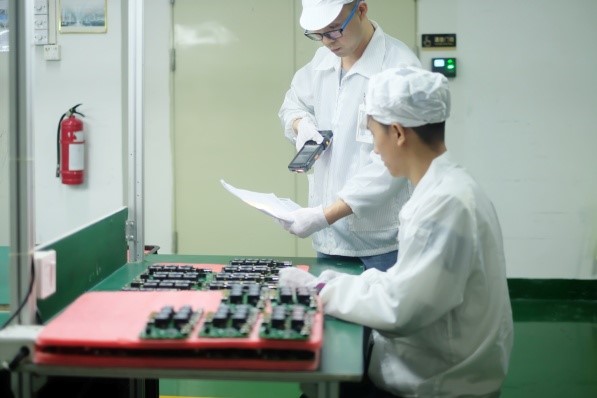 |
|
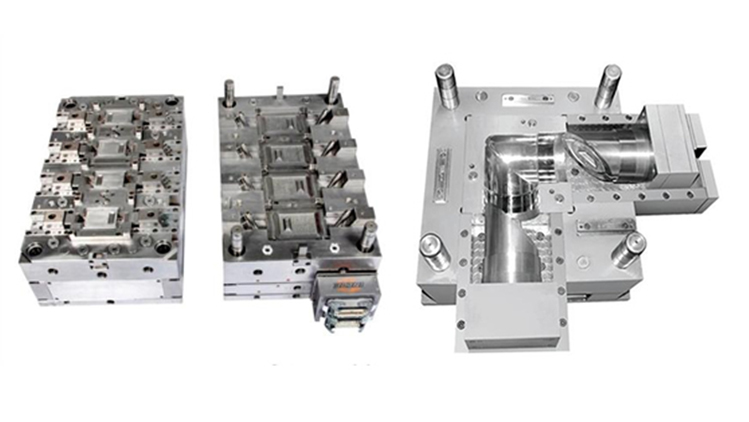 |
Design of Injection Mold
A team with 17 years of senior experience in mold manufacturing, with years of experience in product design, mold design, and precision parts production for well-known brand enterprises; Through pre technical review and DFM, fully understand the product's characteristic requirements. Led by the Engineering Department and the Mold Department, conduct thorough pre evaluation of product functionality to ensure that product functionality, structure, and appearance meet customer needs. |
|
Test strategy development
Integrating computer generated product design with computer controlled machining stations is fundamental to precise tooling construction. Alliance uses the most advanced CAD/CAM equipment to build molds, so they are created fast and accurately. Design files are translated into three-dimensional geometric tool cutting paths, while CAM (computer aided machining) streamlines the manufacturing process to provide rapid prototyping and the final production mold. CAD-driven electric discharge machines cut intricate shapes that conventional milling machines cannot achieve. |
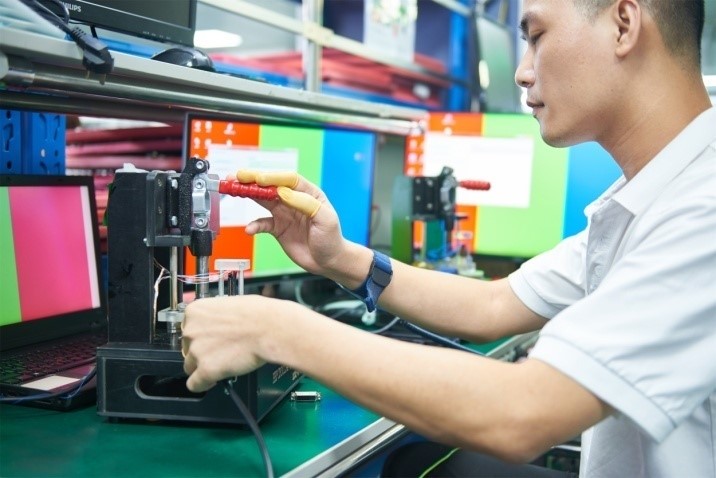 |
|
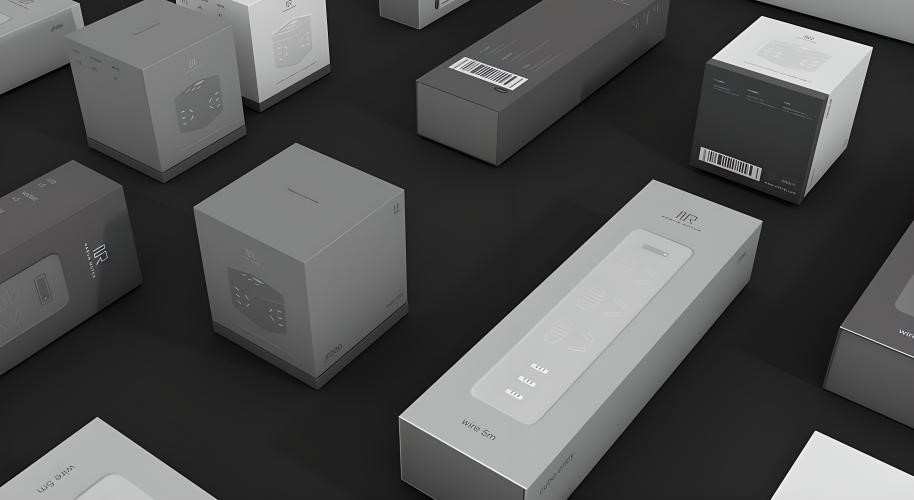 |
Packaging
Our design team provides design of packaging according to specified product features, transportation method and different market needs. |
|